From Concept to Production: 5 Key Steps to Manufacturing Your Electronic Device

Unlike software, hardware development is long and costly. Hardware startups looking to bring their electronic device to mass production need to have a clear understanding of the number of key processes involved. TechDesign gives you the lowdown below:
1) Concept Refinement
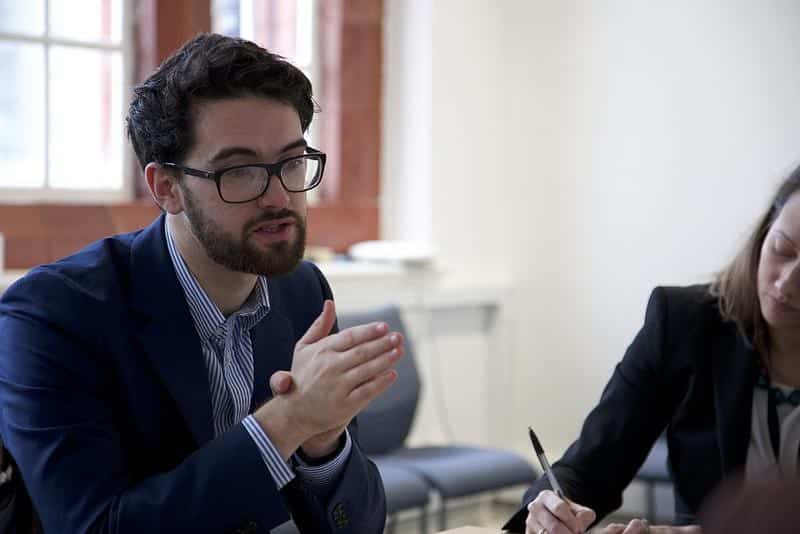
The concept refinement stage is where you flesh out the basic idea of what you want your product to be and how it will meet the needs of consumers. Try to draw sketches and notes of your initial concept.
Before even starting with the technological aspects of your electrical product, you need to engage in serious problem research. For those from engineering backgrounds, you may want to jump into the ‘how’ questions regarding to the building and manufacturing of your device. However, the emphasis here should be more on the ‘what’, ‘who’ and ‘why’ questions related to your electronic device: Who are the people having this problem? What are their needs? Why will your product solve their problems? The ‘five whys’ technique is a great set of tools for startups to utilize.
After brainstorming the answers to these questions, you need to test your assumptions by doing market research. There are two main types of market research that you will need to consider:
1. Problem Research: This is where you consider the user personas and their wants and needs in regards to the areas surrounding your product. Ideally you will start with qualitative research methods such as interviews or focus groups. Remember you are trying to eradicate your own bias and to understand your consumers, rather than pitching the product. Inc.com produced an excellent primer on qualitative research for startups.
2. Solution Research: This is performed when the idea is better formed but no concrete plans have been put in place. Here you would show mockups and prototypes to get ideas from consumers regarding functionality and features.
After conducting an extensive period of research, you should have a clear value proposition to your consumers that will form the bedrock for nailing down the features for your electronics device.
2) Proposal Preparation
At this stage, the team should be able to crystalize and define the MVP (Minimal Viable Product) which will be used in the following engineering and manufacturing stages.
One of the key steps to asserting the feasibility of your device is to put together what is known as a “duct tape prototype”. These quickly put together prototypes work somewhat like the final product put look nothing like it. The emphasis is to test for basic technical viability and human economics. One way to expedite this process is to purchase a development kit from companies selling a key component.
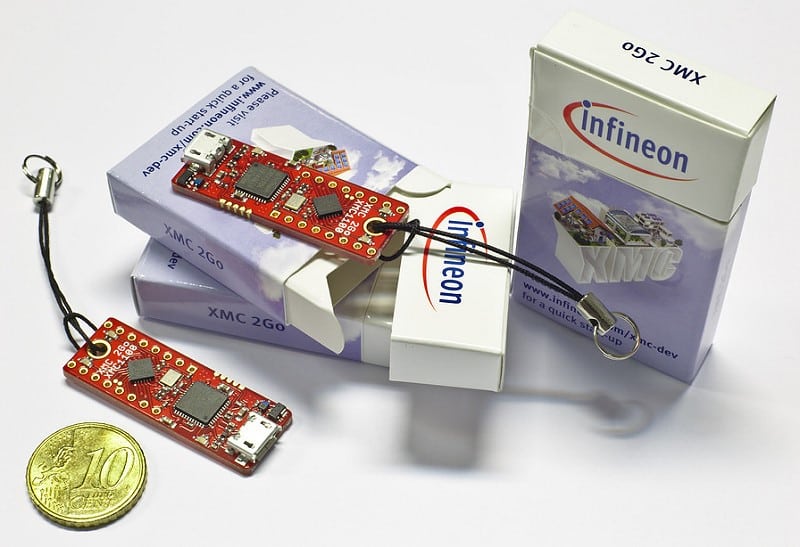
Once you have proven feasibility for the product, you can start to put together a Product Requirements Document (PRD) which will contain all of the functional specifications for the MVP. The Silicon Valley Group have put together an excellent guide for startups writing a PRD. You don’t need a 300 page document, but your PRD should contain the following:
● Product Purpose: Who your consumers are and what are their problems and usage scenarios.
● Features: Clear specifications and requirements that are explained in enough details that the team can understand themselves.
● Release Criteria: A list of the true minimum requirements for final product release.
● Schedule: A realistic timeframe for each milestone and project completion.
3) Prototype Development
If all of your questions regarding the meeting of market needs, technical feasibility has been answered and you have a workable PRD, it’s time to create a true ‘looks-like, works-like’ prototype. A prototype allows you to have something to show to VC’s and potential customers.
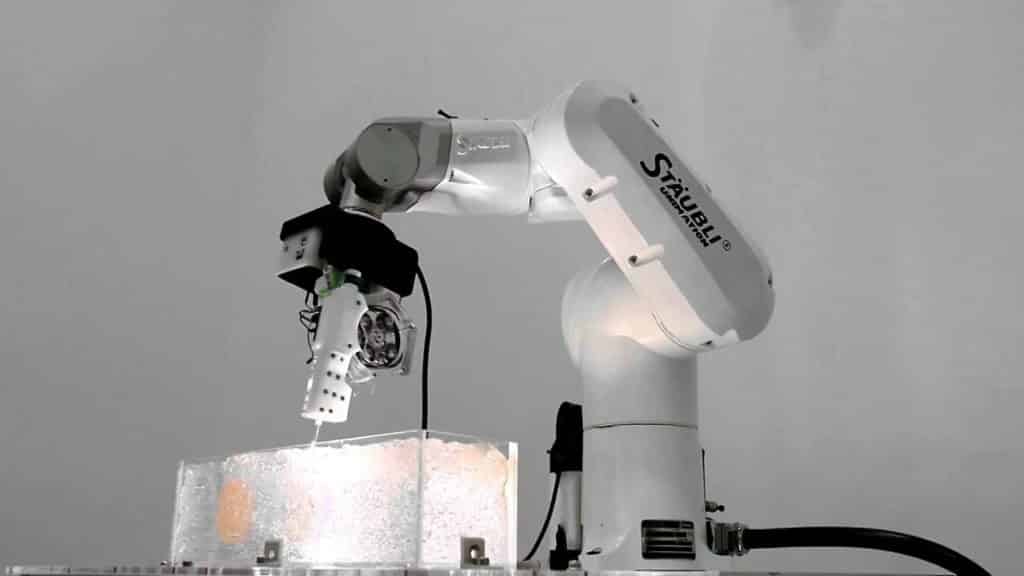
4) Testing and Refinement
Your product should now be three major iterations or less from a mass-production worthy design. There are three main engineering validation stages:
● EVT or Engineering Validation and Testing
The EVT build is an iteration of the engineering prototype in which all of the functional requirements are matched and the testing results meets the requirements outlined in the PRD. The PCB for the hardware will be tested for thermal, power and EMI stresses. Units must be completely functional and testable and made from the materials intended for the final product. The final exit criteria for this stage is configuration of the design that meets the required standards for functionality, performance and reliability.
● DVT or Design Validation and Testing
In this stage, all of the hardware is complete and your aim is to make sure that your product matches your requirements in terms of cosmetics and environment. This stage is also where tools are developed and inspected. You are aiming to teach the contract manufacturer how to build your product while at the same time identifying remaining DFM (design for manufacturing) issues. You will be producing small batches of your product and putting it under real stresses such as dropping from a height, burning it or seeing if it is waterproof.
In this step, you will make sure that your product meets the certification and standards procedures for target countries that you plan to sell your electronic device to. Certifications include CE, RoHS, FCC and UL.
● PVT or Production Validation and Testing
Your product is nearly ready for mass production, but there is one final stage of testing. The PV iteration will see tests of the manufacturing processes devised in the course of the EVT and DVT phases. In PVT, the units you are building should be ready to sell to customers if they pass all of the test stations. A pilot production line will be established to check if there are any failures at any stage of the production line. At the end of the PVT, the hardware startup and contract manufacturer will decide whether or not to move on to mass production.
5) Mass Production
Finally, you have reached your target! You still need to be actively looking for fixing issues in the design and manufacturing process. Over the following six to nine months, continue testing of your product at a high sampling rate and put ongoing reliability tests programs in place. As soon as you are certain that quality issues have been largely addressed, you can ramp up the production capacity to match your original unit forecast.
Let TechDesign Simplify the Process of Manufacturing an Electrical Device
TechDesign allows hardware startups to simplify the hardware development cycle by aggregating all the listed steps through its platform. Circumvent many of the problems associated with bringing an electronic device to market by allowing TechDesign to help match you with an appropriate manufacturer. Rather than having to be bogged down with dealing with multiple companies and people, with TechDesign we offer a single contact window for managing all of the complex development cycles involved with developing your electronics device.
Get a free quote for your project today.
Sign up to become TechDesign member and get the first-hand supply chain news.